Contaminated fluid is the cause of most failures in hydraulic equipment. Using contaminated hydraulic fluid also has other negative effects, such as accelerating wear and tear, which leads to a drop in machinery operating rates.
The YAMASHIN Group’s industrial filters prevent equipment failures and help maintain operating rates by removing contaminants so that internal systems are always clean.
We supply various types of hydraulic fluid filters to suit different applications.
As shown in the diagram below, placing the filter in the best possible position in a line removes contaminants, which can cause equipment failure.
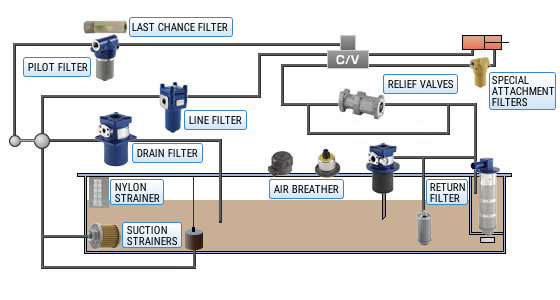
Pilot filters
Used in hydraulic pilot lines, which include line control valves.
Control valves are protected by the filter, which manages the level of contamination in the pilot lines.
Selecting the best filter for the contaminant tolerance of hydraulic components in the line is important.
Last chance filters
As the name suggests, these filters are installed as last chance filtration devices to protect particularly important hydraulic components.
The filters are installed in supply lines and need to withstand the high pressures of fluid discharged from pumps. To meet these requirements, the filters are usually compact and use wire mesh filtration media.
Line filters
Installed in hydraulic supply lines on the discharge side of pumps.
It is important to select the best filter for application, line pressure and flow rate.
Relief valves
Used to protect hydraulic lines and components by releasing pressure when the line design limits are reached.
Our LV series is used widely in relief valve applications for oil coolers.
Special attachment filters
Installed in return lines as special attachments to circuit breakers and other components.
Used to remove contaminants that may enter lines during special work on hydraulic lines.
Drain filters
Installed in pump drain lines.
Easy-to-replace spin filters are used in many cases due to the low-pressure, low-flow conditions of drain lines.
Air breathers
Used to maintain the purity of fluid stored in hydraulic reservoirs by preventing airborne pollutants from entering the reservoir as a result of changes in fluid volume.
Our AB series is used widely in pressurized reservoirs as they can maintain pressure in exhaust ports.
Nylon strainers
Installed in filler caps to prevent contaminants from entering reservoirs during filling.
Filtration media is coarser, as the nylon strainers are designed to remove relatively large contaminant particles. The strainers are also positioned in order to prevent fluid from overflowing during filling.
Suction strainers
Installed in front of pump suction ports to protect pumps.
Suction filters need to have low pressure loss to prevent cavitation in the pump. Our filters are designed to meet that requirement with a pleated metal mesh that significantly increases the filtration area.
Return filters
Installed in hydraulic return lines to filter fluid before it returns to the reservoir.
Most return filters need to be changed regularly, as they are used to clean all the fluid inside the hydraulic circuit. Maintainability is therefore an important consideration.
We supply a wide range of highly efficient, compact and long-life (high capacity) return filters designed for various applications.
The majority of our filters need to be replaced.
During use, filter lines can become blocked with contaminants, leading to significant drop of pressure. Filters should therefore be replaced as needed to ensure optimum filtration performance.
The timing of filter replacement depends on various conditions, such as the application environment and the type of fluid used, but a good benchmark is pressure drop.
Pressure drop |
0.1Mpa~0.15Mpa(1.0~1.5kgf/cm2) |
---|
Time in use |
1,000hrs |
---|